Buying a new autoclave
by Jane Renehan
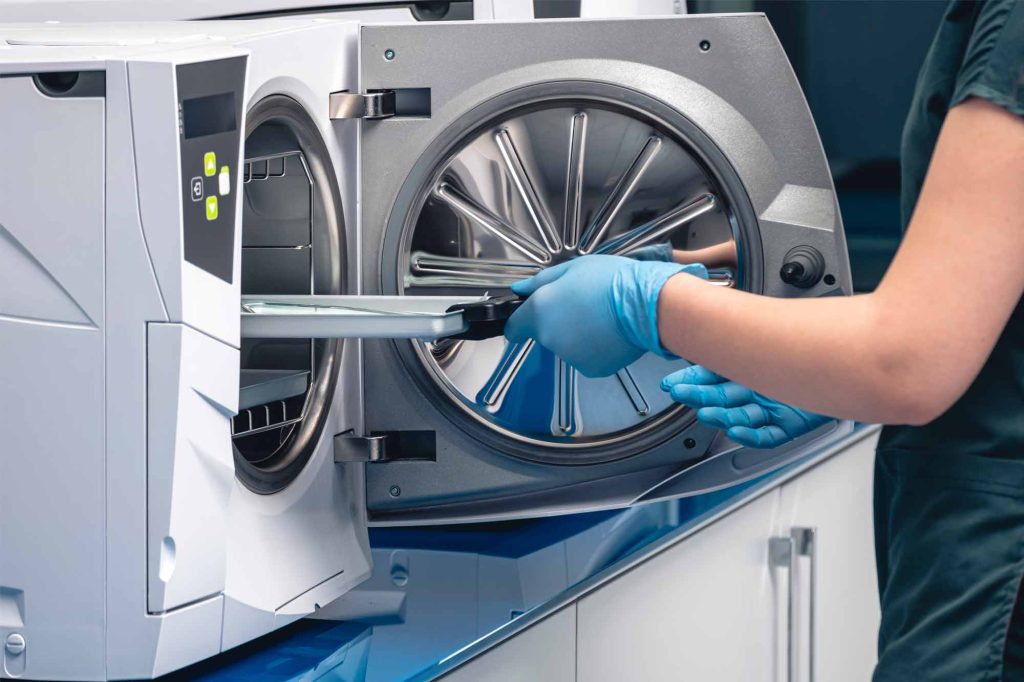
Jane Renehan offers 10 tips to follow when buying a new autoclave in response to a reader’s question.
The question – Dear Jane…
Can you give me some advice as to what I should look out for when buying a new dental autoclave?
The answer
The autoclave is an essential equipment item in dental practices. It must be reliable and fit for purpose. Anything less will cause disruption and expense.
Here are my 10 tips for anyone considering the purchase of a new autoclave:
1. Chamber dimensions
I recommend investing in the largest chamber possible. Small chambers sterilise fewer bags of instruments, they are easier to overload and therefore have more failed cycles. This can lead to process inefficiency and instruments not being sterilised.
2. Type B class
These autoclaves are recommended, as they are capable of sterilising all loads including bagged and hinged instruments, lumens (handpieces) and porous loads. If you have only one autoclave, then have a B class.
3. Water
The Dental Council Code Of Practice relating to infection prevention and control (section 3.2.3) states: ‘High-quality water (e.g. deionised, distilled, reverse osmosis) as advised by the manufacturer, must be used in autoclaves.’
I prefer a directly plumbed reverse osmosis supply or deionising water cartridges. Either of these systems allows for consistency in quality and reduces time taken to manually fill the freshwater storage tank. In-house manufacturing of distilled or reverse osmosis water can have drawbacks, such as storage, capacity, quality, and expense.
4. Space and ventilation
Confirm you have sufficient counter-top space for your new autoclave, both depth and height. If your intention is to contain it within cabinetry or a recessed area, you must allow for dissipation of heat and adequate room for servicing. Most autoclave doors are left hinged. Check if this may be a problem for your staff taking out hot trays of instruments at the end of the cycle.
5. Utilities and wastewater
Consider the utilities required to support the autoclave. Electrical sockets directly behind the unit are difficult to access. Modern autoclaves usually have moulded plugs, so the socket needs to be placed higher than normal above the countertop. Try to place the socket to the side of the autoclave. It’s a good idea to plumb the wastewater tank drainage outlet as this saves time and reduces water spillages.
6. Data recording
When sterile instruments are removed from the autoclave, the ‘success parameters’ of time, temperature and pressure must be checked and recorded. Only when the parameters are successful can the load be released for use on another patient.
There are three different data recording systems. A data logger such as a CF card or USB memory stick has the advantage of gathering and storing the data. The disadvantage is unless the system is linked to a monitor in the decontamination room, it’s not always easy to see the results at the end of each cycle.
Printers are excellent for reading the cycle parameters in a timely manner. However, there are the practical issues of replacing ink cartridges and paper rolls.
The third system is an inbuilt display monitor linked to a logger or printer. This allows the dental nurse to visually check the parameters and have the back up of recorded results.
7. Installation and running costs
Installation and initial set-up must comply with the Dental Council Code Of Practice relating to infection prevention and control.
Section 3.2.6.1 states: ‘When an autoclave is purchase it must be commissioned by a competent person and commissioning documents must be given by the supplier to the purchaser.’
Therefore, enquire if commissioning is included in the purchase price. The Code Of Practice (section 3.2.6.2) also requires that an annual validation is carried out by a competent person. Look into running costs such as servicing, parts availability, and warranty.
The manufacturers’ recommended periods between servicing can vary from annual, to biennial (two-yearly), or three-yearly. Some autoclaves require servicing at 1,000 cycles others can go up to 4,000 cycles before servicing is recommended.
In addition to annual validation and routine servicing, regular pressure vessel checks are required at least every 14 months (S.I. No. 445 of 2012).
8. Compliance
Purchase your autoclave from a reputable dental supplier. B class dental autoclaves are medical devices complying with European standard EN 13060 (small steam sterilisers). The identification plate contains specified items of information, most importantly the CE-mark accompanied by the European registration number.
Be aware of the Brexit factor. In the coming months, Great Britain will cease using the CE-mark, moving instead to a new UKCA marking on manufactured goods.
9. Research
It pays to do some background reading in advance of your purchase. Compare the technical specification of your preferred units under the headings of energy use, sound emission, and functionality. Don’t be rushed by special offers or financial incentives.
In an emergency situation where your autoclave dies, it’s worth asking your supplier if they can loan you an autoclave for the short time while you are deciding and awaiting the delivery of your preferred unit. In truth, most dentists know very little about the day to day working of an autoclave. Consult your dental nurses and include them in your decision.
10. Finally
I recommend that you aim in the first instance at buying quality and then consider if the price is right. You won’t go wrong by following the principle of always buying the best you can afford.
Read more Dear Jane articles: